Esta calculadora para sacar una escuadra te va ha facilitar obtener las medidas que necesitas para:
- Sacar una escuadra de un terreno
- Sacar una escuadra de una habitación
- Sacar una escuadra de una casa
- Sacar una escuadra de un suelo
- Sacar una escuadra de un piso
- Sacar una escuadra de un techo
Esta calculadora para sacar una escuadra te va ha facilitar obtener las medidas que necesitas para:
- Sacar una escuadra de un terreno
- Sacar una escuadra de una habitación
- Sacar una escuadra de una casa
- Sacar una escuadra de un suelo
- Sacar una escuadra de un piso
- Sacar una escuadra de un techo
Ya puedes usar la Calculadora para Escuadras. EMPEZAMOS!!
👉
👉
🏆
Medidas para sacar una escuadra. EMPEZAR YA!!
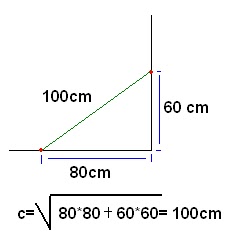
Este método se utiliza para hacer una escuadra de albañil o de obra. Es una escuadra hecha con perfiles metálicos soldados o con listones de madera con clavos. Los perfiles, que serian los lados, tiene 1 metro cada uno. Si haces la operación en la calculadora, te da la diagonal 141 cm. Con esa medida sería una escuadra perfecta.
" Carretillas Elevadoras en la Soldadura " 👈
Consejo: Si la construyes con perfiles metálicos, ten cuidado al soldarla, se suelen deformar dando errores al querer sacar la escuadra de la obra.
Como sacar una escuadra con el metro
En la construcción y replanteo de terrenos, es esencial contar con herramientas precisas para garantizar una correcta ejecución del proyecto. Una de estas herramientas es la escuadra, que nos permite obtener ángulos rectos perfectos. En este artículo, le explicaremos cómo sacar una escuadra con el metro para el replanteo de un terreno.
¿Qué es una escuadra?
La escuadra es una herramienta de medición compuesta por dos piezas rectangulares unidas en un ángulo recto. Se utiliza para medir y marcar ángulos rectos perfectos, esenciales en la construcción y replanteo de terrenos.
Paso a paso para sacar una escuadra a 90 grados
Para sacar una escuadra a 90 grados, necesitaremos los siguientes materiales:
- Dos piezas rectangulares, como por ejemplo, dos listones de madera o dos reglas.
- Una cinta métrica.
- Un lápiz.
Siga estos pasos para sacar una escuadra a 90 grados:
- Tome una de las piezas rectangulares y colóquela en posición vertical sobre el terreno que desea replantear.
- Mida con la cinta métrica una distancia de 3 unidades hacia la derecha desde la parte inferior de la pieza que acaba de colocar. Marque este punto con un lápiz.
- Desde este punto, mida una distancia de 4 unidades hacia arriba y marque el punto con un lápiz.
- Ahora, tome la segunda pieza rectangular y colóquela en posición horizontal, apoyándola en el punto que acabamos de marcar en el paso anterior.
- Mueva la segunda pieza hacia la derecha o hacia la izquierda hasta que se alinee perfectamente con la pieza vertical.
- Una vez que las dos piezas estén alineadas, compruebe que la distancia entre el extremo inferior de la pieza vertical y el extremo derecho de la pieza horizontal mida exactamente 5 unidades.
- Si las medidas son correctas, habrá sacado una escuadra a 90 grados.
Es importante destacar que para obtener una medida precisa, debe asegurarse de que las piezas sean rectangulares y estén en buenas condiciones. También es recomendable comprobar la precisión de la escuadra utilizando un nivel de burbuja.
Sacar una escuadra a 90 grados es un procedimiento sencillo pero fundamental para el replanteo de terrenos y la construcción en general. Al seguir los pasos descritos en este artículo, podrá obtener una escuadra precisa y garantizar la correcta ejecución de su proyecto.
¿Que es el método 3, 4 y 5?
Ya veis, una simple formula con más de 2000 años nos ha sacado del apuro, gracias Pitágoras.
- Teorema de Pitágoras fórmula
- Triángulo Rectangulo
- Hipotenusa
- Pitágoras fórmula
- Como sacar una escuadra con metro
- Escuadra 30 40 50
- Escuadra albañil
- Escuadra de obra
- Medidas para sacar una escuadra
- Como sacar escuadra terreno
- Replanteo de obra
- Como hacer una escuadra
- Escuadra de angulos
![]() |